
Condition Monitoring
Condition Monitoring (=Zustandsüberwachung) beschreibt den Prozess der Überwachung eines Zustandsparameters in einer Anlage oder Maschine. Zum Beispiel können Vibrationen, Temperatur, Luftqualität usw. automatisiert werden, um signifikante Änderungen zu erkennen, die auf einen sich entwickelnden Fehler hinweisen. Sie ist ein wesentlicher Bestandteil der vorausschauenden Instandhaltung. Der Einsatz von Zustandsüberwachung ermöglicht die Planung von Wartungsarbeiten oder das Ergreifen anderer Maßnahmen zur Verhinderung von Folgeschäden und deren Konsequenzen. Einzigartig an der Zustandsüberwachung ist der Vorteil, dass Bedingungen, die die normale Lebensdauer verkürzen würden, behandelt werden können, bevor sie sich zu einem großen Ausfall entwickeln. Zustandsüberwachungstechniken werden typischerweise bei rotierenden Anlagen, Hilfssystemen und anderen Maschinen (Kompressoren, Pumpen, Elektromotoren, Verbrennungsmotoren, Pressen) eingesetzt, während periodische Inspektionen mit zerstörungsfreien Prüfverfahren (NDT) und Fitness-for-Service (FFS) Bewertungen für statische Anlagen wie Kessel, Rohrleitungen und Wärmetauscher verwendet werden.

Prozessfertigung
Die Prozessfertigung ist ein Bereich der Fertigung, der mit Formeln und Herstellungsrezepten verbunden ist und im Gegensatz zur diskreten Fertigung steht, die sich mit diskreten Einheiten, Stücklisten und Baugruppen befasst. Die Prozessfertigung ist in Branchen wie Lebensmittel, Getränke, Chemie, Pharmazie, Nahrungsergänzungsmittel, Konsumgüter, Cannabis und Biotechnologie verbreitet. Genau wie die von ihnen hergestellten Produkte haben diskrete und prozessorientierte Fertigungssoftware unterschiedliche Schwerpunkte und lösen unterschiedliche Probleme. Aus demselben Grund, warum das sprichwörtliche eckige Pegel nicht in das runde Loch passt, wird Software, die auf diskrete oder sogar hybride Fertigung ausgerichtet ist, nicht reibungslos in einer prozessorientierten Fertigungsumgebung funktionieren. Bei der Prozessfertigung kann das Endprodukt nicht in seine ursprünglichen Bestandteile zerlegt werden, zum Beispiel Bier oder Pastasauce. Daher muss die Software in der Lage sein, diese Feinheiten zu berücksichtigen und Rohstoffe in fertige Produkte umzuwandeln. Kritische Aspekte wie Rezeptformulierung, Vorwärts- und Rückwärts-Rückverfolgbarkeit von Chargen, Handhabung gemischter Maßeinheiten und Umrechnung, Berechnungen von Rohmaterialien sowie skalierbare Chargenprotokolle mit Versionsverfolgung und Aufzeichnung von Herstellungsschritten und Produktionsnotizen sind spezifisch für prozessorientierte Hersteller und wesentliche Funktionalitäten von Prozessfertigungssoftware.
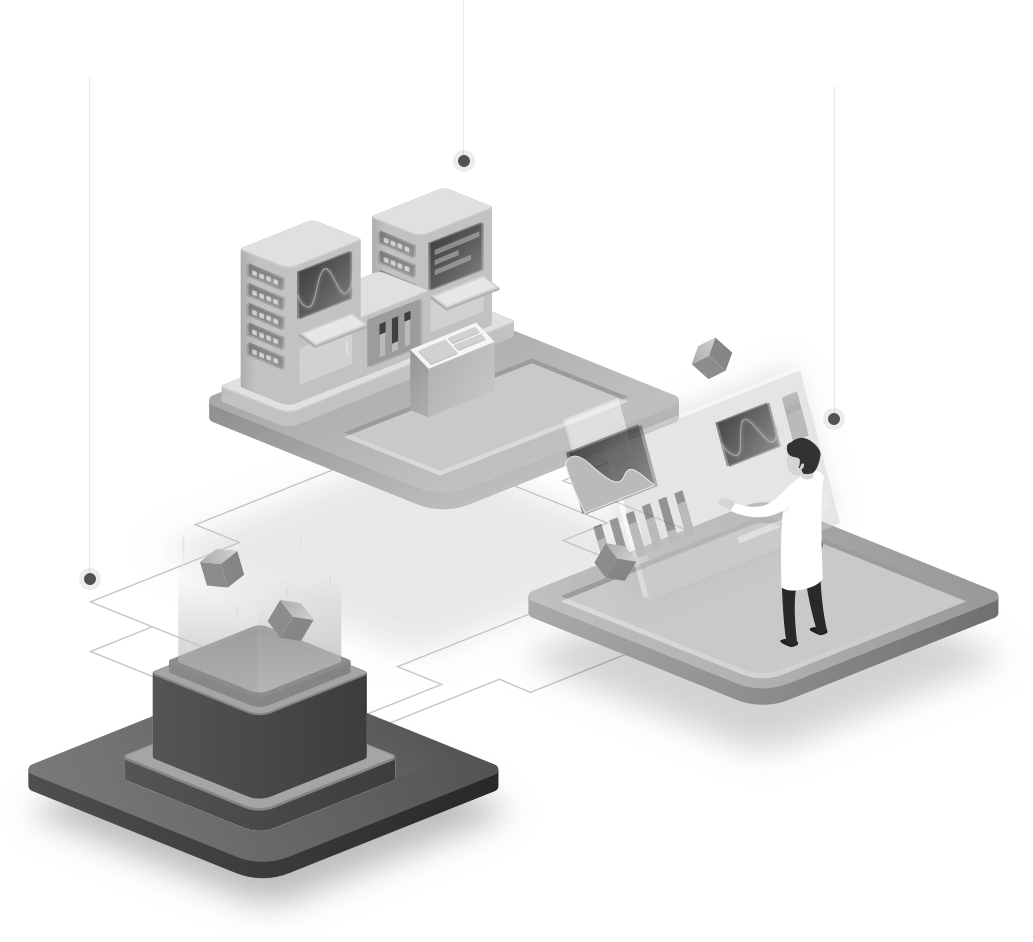
SCADA
Die Überwachung und Steuerung von Prozessen (englisch Supervisory Control and Data Acquisition, SCADA) ist eine Architektur für Steuersysteme, die Computer, vernetzte Datenkommunikation und grafische Benutzeroberflächen (GUI) für die übergeordnete Prozesssteuerung umfasst, aber auch andere Peripheriegeräte wie programmierbare Logikcontroller (PLCs) und diskrete proportional-integrale-differenzielle (PID) Regler zur Schnittstelle mit Prozessgeräten oder Maschinen einschließt. Die Verwendung von SCADA wurde auch für das Management und die Durchführung von projektorientierten Prozessen in der Bauindustrie in Betracht gezogen.
Die Bedienoberflächen, die die Überwachung und die Ausgabe von Prozessbefehlen ermöglichen, wie beispielsweise Änderungen des Regelungssollwerts, werden vom SCADA-Computersystem gehandhabt. Die auf niedrigerer Ebene durchgeführten Operationen, wie Echtzeit-Steuerungslogik oder Reglerberechnungen, werden von vernetzten Modulen durchgeführt, die mit den Feldsensoren und -aktoren verbunden sind.
Das SCADA-Konzept ist darauf ausgelegt, einen universellen Remotezugriff auf eine Vielzahl lokaler Steuerungsmodule zu ermöglichen, die von verschiedenen Herstellern stammen können, und den Zugriff über standardisierte Automatisierungsprotokolle zu ermöglichen. In der Praxis haben sich große SCADA-Systeme entwickelt, die in ihrer Funktion sehr ähnlich sind wie verteilte Steuersysteme, jedoch mehrere Möglichkeiten zur Schnittstelle mit der Anlage nutzen. Sie können groß angelegte Prozesse steuern, die mehrere Standorte umfassen, und über große und kleine Entfernungen hinweg arbeiten. Trotz Bedenken, dass SCADA-Systeme anfällig für Cyberkrieg/Cyberterrorismus-Angriffe sind, sind sie eine der am häufigsten verwendeten Arten von industriellen Steuersystemen.
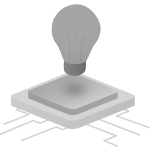
Alarmierung und HMI
Im Bereich des Industriedesigns der Mensch-Computer-Interaktion ist eine Benutzeroberfläche (englisch User Interface, UI) der Raum, in dem Interaktionen zwischen Menschen und Maschinen stattfinden. Das Ziel dieser Interaktion besteht darin, dem Menschen eine effektive Bedienung und Steuerung der Maschine zu ermöglichen, während gleichzeitig die Maschine Informationen zurückgibt, die den Entscheidungsprozess des Bedieners unterstützen. Beispiele für dieses breite Konzept von Benutzeroberflächen sind die interaktiven Aspekte von Computer-Betriebssystemen, Handwerkzeugen, Steuerungen für schwere Maschinen und Prozesssteuerungen. Die bei der Gestaltung von Benutzeroberflächen zu berücksichtigenden Aspekte stehen im Zusammenhang mit oder beziehen sich auf Disziplinen wie Ergonomie und Psychologie.
Im Allgemeinen besteht das Ziel der Benutzeroberflächengestaltung darin, eine Benutzeroberfläche zu schaffen, die es einfach, effizient und angenehm (benutzerfreundlich) macht, eine Maschine so zu bedienen, dass das gewünschte Ergebnis erreicht wird (d. h. maximale Benutzerfreundlichkeit). Dies bedeutet im Allgemeinen, dass der Bediener minimale Eingaben machen muss, um das gewünschte Ergebnis zu erzielen, und dass die Maschine auch unerwünschte Ausgaben für den Benutzer minimiert.

Predictive maintenance
Die Techniken der „Predictive maintenance“ sind darauf ausgelegt, den Zustand von Assets im Betrieb zu bestimmen, um abzuschätzen, wann Wartungsarbeiten durchgeführt werden sollten. Dieser Ansatz verspricht Kosteneinsparungen gegenüber routinemäßiger oder zeitbasierter präventiver Wartung, da Aufgaben nur bei Bedarf durchgeführt werden. Daher wird er als zustandsbasierte Instandhaltung betrachtet, die auf Schätzungen des Degradationszustands eines Gegenstands basiert.
Das Hauptversprechen der vorausschauenden Instandhaltung besteht darin, eine bequeme Planung von korrektiven Wartungsarbeiten zu ermöglichen und unerwartete Ausfälle von Geräten zu verhindern. Der Schlüssel dazu liegt in „richtigen Informationen über die Lebensdauer der Ausrüstung, erhöhter Anlagensicherheit, weniger Unfällen mit negativen Umweltauswirkungen und optimierter Ersatzteilverwaltung“.
Die vorausschauende Instandhaltung unterscheidet sich von der präventiven Instandhaltung dadurch, dass sie sich auf den tatsächlichen Zustand der Ausrüstung stützt, anstatt auf durchschnittliche oder erwartete Lebensstatistiken, um vorherzusagen, wann Wartungsarbeiten erforderlich sind. Typischerweise werden maschinelles Lernen und ähnliche Ansätze eingesetzt, um den tatsächlichen Zustand der Ausrüstung zu definieren und ihre zukünftigen Zustände vorherzusagen.